Pavement Management Systems
Rate Pavement Networks with Collected IRI, Rutting, Macrotexture and Image Distress Processing
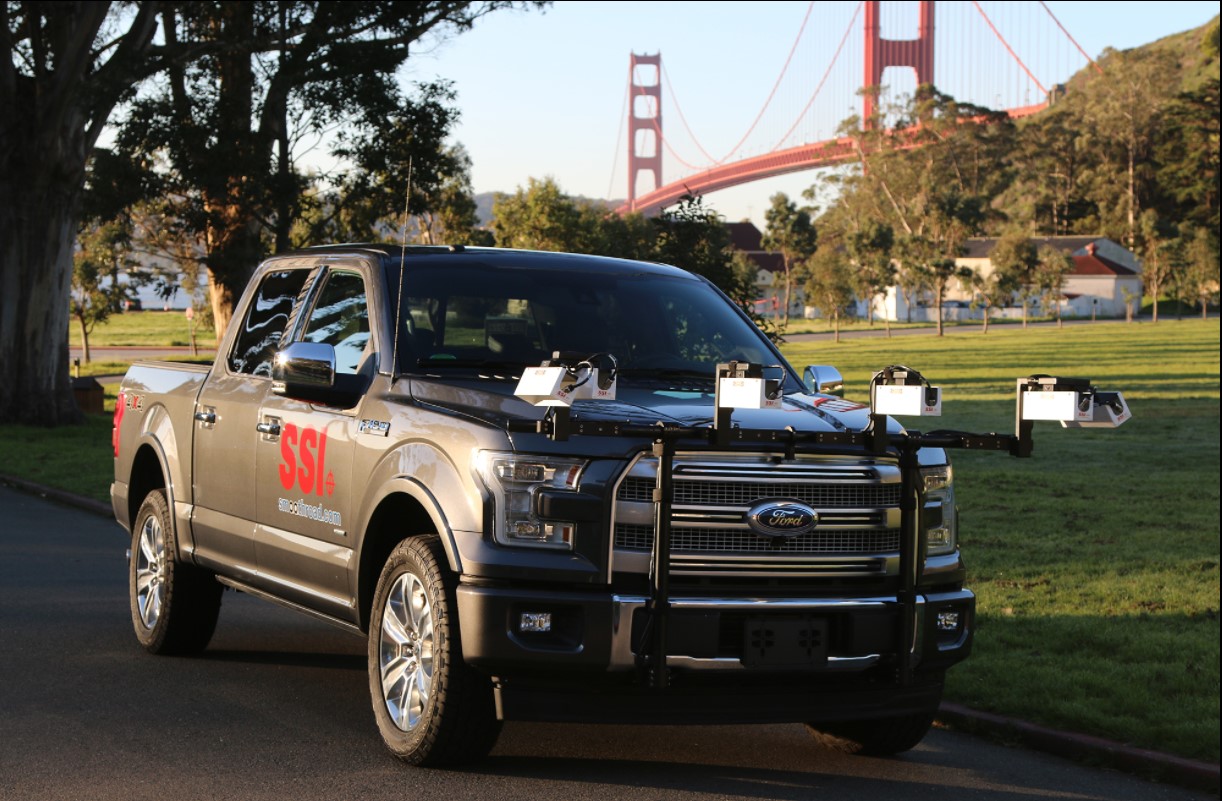
Use an SSI system to collect ride quality profiles, rutting, macrotexture, cross-slope, and use ROW images to classify distresses.
Collect Pavement Networks Automatically
Use existing shapefiles or KML paths of the pavement network to display the routes to collect. SSI Profiler software can match the collected paths to the network segments. This feature can be paired with any SSI inertial profiler system.
SSI’s Network Manager software accepts shapefiles or KMLs for the segment paths. The segments that were already collected have a different path color to differentiate them from the uncollected areas.
View the statistics for each run paths IRI or PRI, defects (straightedge), macrotexture, rutting, and image distress score. The data can be reported as an overall average for the segment or as an interval (528-feet or 100 meter). All of the data is available immediately, except for the image distress score which requires image processing.
Images are captured every 20-feet while collecting data. These images are processed for a distress score over the 20-foot span. This image score is report for each image. In the KML the 20-foot span is report as color-coded. The Excel export reports the worst image rating for the path segment.
Customize your export to Excel using data entered into the SSI Profiler parameters, shapefile, or collected data. Update your network conditions as new data is collected.
Scalable System
SSI designs equipment to be modular, installed in the field, and simple to upgrade. You may start with a dual laser profiler for IRI and build on this system with texture and rutting sensors. SSI can even integrate LCMS or GPR sensors for higher-end pavement management systems.
SSI recommends the Zero-Speed inertial profiler upgrade for any urban pavement network. The advantage is that the Zero-Speed system allows for stop-and-go collections. There will not be large errors and speed drop-outs at low speeds. This has plagued all network collection devices and inertial profilers in the past. The SSI Zero-Speed inertial profiler can collect accurate data through stoppages under AASHTO r56 and r57.
First-Tier Pavement Management
The simple system for urban areas would be a dual laser Zero-Speed inertial profiler, like the CS9100/CS9300 Zero-Speed. This system will collect IRI profiles in each wheelpath with cross-slope and ROW images at a user-specified interval. Macrotexture is an option in one or both wheelpaths. The operator can use Network Manager to collect the segment paths of the network and use ROW images to add a distress score.
Second Tier Pavement Management
The mid-level pavement management system includes all of the features of the first tier, but also adds rutting measurement. This system would be the CS9500 Zero-Speed and can collect IRI in the wheelpaths, rutting per AASHTO PP69, macrotexture, ROW camera images, and cross-slope. The CS9500 system is run off of a Panasonic Toughbook laptop. The ROW images can be used to get a distress score.
Top-Tier Pavement Management
When PCI measurement is a requirement the pavement distresses need to be measured and classified. This requires a high frequency scanning laser like the LCMS sensor. These systems will have large data processing and storage needs.
Accurate Rutting, IRI, and Texture
The SSI systems can all use the Network Manager software – from dual laser profilers to the CS9500 Full Lane Survey Profiler. The data collected by each system can be exported to GIS or Excel to import into the agencies pavement management software. Excel templates for this import are available from SSI.
The network management systems can be outfitted with sensors for full lane rutting, 5-point rutting, or 3-point rutting along with IRI, ROW cameras, and texture (MPD, ETD, RMS).
Use Imagery to Detect Distresses
SSI also has a simple pavement management option to rate your roads. Export a pavement score based on the collected data to classify your collections based on ride values, rutting and a processed image score. The report can be processed instantaneously after a collection. The image score can follow the PASER rating system, which can be found here. SSI can import results from multiple AI image processing vendors.
The image ratings can be paired with the profiler measurements or exported on their own to create a Google Earth KMZ heatmap of the road quality. Multiple lanes can be reported together with SSI’s high quality GPS receivers.
IRI Smoothness
SSI recommends a Zero-Speed system for pavement management rating. The Zero-Speed system is proprietary to SSI. It eliminates large IRI and profile measurement errors at low speeds and stoppages. This allows for the collected profiles to be accurate depictions of your pavement network.
All of SSI systems have the capability of collecting IRI or MRI smoothness profiles. Starting at the simple inertial profiler level, agencies can collect smoothness data on every lane of their network at a very low cost relative to full scale pavement management.
The benefit is the data reflects the ride quality of the traveling public. An inertial profiler can detect pavement distresses that affect elevations (faulting, potholes, utilities, rutting).
The inertial profiler will not detect the severity of the PCI index for bleeding, weathering, or the extent of cracking. The system will only detect changes in elevation reflected in the ride value.
Rutting
With a 3-point, 5-point, or full lane transverse profiler system can detect ride value smoothness and rutting. The rutting sampling interval can be every inch or greater with the 3- or 5-point systems, but can be collected as low as 5mm x 5mm at slow speeds with the CS9500 or lidar systems. Usually rutting is reported at a 2-inch (50mm) longitudinal sampling interval at highway speeds.
Cameras
Right-of-way (ROW) and downfacing cameras can be used on all SSI systems. These cameras are triggered by SSI software and embedded within the SSI Profiler program. SSI offers camera options from 5MP to 24MP.
Texture
Texture can be collected with a high frequency dot laser or a line laser. The elevation data reported can be converted into MPD, ETD, or RMS reports for each sample. More research is being conducted into the micro and macro texture readings of lasers to determine correlation to skid test numbers.
Additional Sensors
SSI is also an integrator of new technology. If you have a new requirement or sensor to implement, SSI can incorporate it. We always use the most accurate and economical equipment for the application.
Typical PCI systems require LCMS sensors for high frequency scanning. These sensors can be integrated into your vehicle by SSI for a top-tier pavement management system.
Custom Pavement Management Systems Built For Cities and Counties
Hardware
- Start with a simple dual laser inertial profiler and add options as needed
- Collect data yourselves, saving money over 3rd party Accelerated Pavement Condition Surveys (APCS)
- Systems can be fixed to a truck or portable for multiple vehicles to share
- Use integrated cameras for ROW image logging
- GPS receiver will track position and index roughness by station distance and GPS location
- Identify and rank roughest pavement segments
Software
- Follow segment paths by importing entire pavement network into SSI Profiler’s Network Manager software. The program collects network segments as you drive. See the completed locations on a colored map
- Export data into your network GIS program with segment IRI, rutting, texture, cross-slope, and an optional visual score
- Use SSI’s rating system to calculate an overall pavement score based on multiple weighted characteristics
Includes our standard SSI Profiler features
- Reports IRI, MRI, HRI, PRI, RN, and Localized Roughness (with adjustable bump and dip templates)
- Integration of custom data templates and calculations
- Instant test results and viewing of profile traces and reports
- Outputs longitudinal profile, elevation data, slope, simulated profilograph, raw strip trace, ERD/PPF (for ProVal), and PRO formats
- Multiple trace reporting allows cross-surface analysis of parallel profile traces (patented by SSI)
- Append data to existing files for comparison of original surface condition with corrected surface
- Profile reports and traces available on-screen, in PDF images, Excel (templates supplied), hard copy print out, or electronic formats
- Colorized traces and highlights of bonus/penalty profile areas
- Encrypted raw data for infinite reanalysis with variable parameters
- Data infinitely rewritable with variable analysis parameters (English or Metric units, profile indexes, data filters, localized roughness).
- Troubleshooting
- Embedded PDF user manual in software
- Send Feedback or report issues to SSI staff directly
- Real time diagnostics monitor system health and ease support
- Desktop license supplied for viewing, analyzing, and printing data
- Software updates by self-executing internet download
- On-site customer training and support worldwide
Optional System Configurations
- Single, dual, or three laser IRI system
- Single or dual laser texture reported as MPD, ETD, RMS
- Full lane transverse rutting
- ROW cameras
- Downfacing rear camera
- Military grade IMU
- Cross-slope
- Road geometry
- Medium or High Resolution GPS receiver
- Point Cloud Survey Export
- CS9500 system option can achieve 6mm accuracy over 95% of points
- Over a million pavement surface data points per mile without time consuming post-processing
- SSI can integrate high-frequency scanning sensors for cracking and distress measurement or GPR into your vehicle with NRE.